Tabletkarka pulpitowa TDP 5
TDP 5 to uniwersalna i łatwa w konserwacji tabletkarka formatu pulpitowego, które oferuje zaskakujący poziom prędkości, wydajności i elastyczności. Może być napędzana prądem lub ręcznie i stanowi idealne rozwiązanie dla każdego, kto potrzebuje wysokiej jakości tabletkarki do produkcji niewielkich partii i partii próbnych, co sprawia, że świetnie nadaje się do działów badawczych itp.
Connect with Our Team
If you have a question or would like more details on the Tabletkarka pulpitowa TDP 5, please complete the form below and someone from our team will be in touch with you soon.
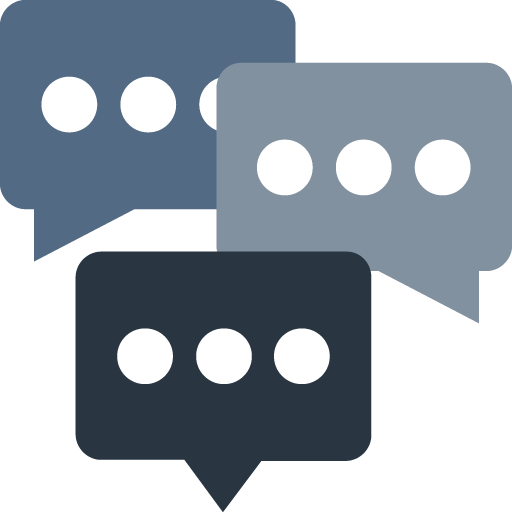
Jeśli poszukujesz tabletkarki, która pomoże Ci opracować nowe tabletki lub będzie służyła do testów konceptualnych przed wprowadzeniem tabletek do produkcji masowej, to TDP5 zdecydowanie będzie świetnym wyborem ze względu na możliwość produkcji różnorodnych tabletek w niewielkich ilościach. Zaprojektowano ją, aby nadawała się do prac laboratoryjnych i badawczych, a nie do produkcji na dużą skalę, jednak mimo tego jest w stanie wyprodukować każdą ilość, od zaledwie kilku tabletek po 5.000 tabletek na godzinę.
Zaletą tej tabletkarki jest uniwersalność połączona z kompleksowym wyposażeniem i wysoka jakość wykonania. To sprawia, że można na niej polegać. Z tych powodów TDP 5 jest często wybierana przez instytuty badawcze, laboratoria, wykorzystywana w technologiach spożywczych, badaniach farmaceutycznych, zakładach chemicznych i szpitalach oraz we wszystkich innych branżach, w których liczy się uniwersalność, łatwość używania i prędkość.
Główne zalety tabletkarki TDP 5:
- Lekka w swojej klasie
- Kompaktowa powierzchnia
- Szybka i niezawodna
- Elastyczna produkcja
- Zasilana elektrycznie lub ręcznie
- Duża kompatybilność z surowcami
- Niskie koszty utrzymania
- Niskie zużycie
- Pracuje z min. 200g surowca
- Wycina tabletki w każdym kształcie
- Możliwa do dopasowania średnica, głębokość i twardość tabletek
- Możliwość wybijania wzorów na tabletkach
- Idealna do wybijania motywów lub produkcji ciągłej
Cechy
TDP 5 to tabletkarka o pojedynczym wybijaku, o maksymalnej sile nacisku wynoszącej 50 kN. Zaprojektowano ja w taki sposób, aby można ją było zamontować na stole warsztatowym, ale można ją z łatwością odłączyć i zamontować w innym miejscu. Oferuje możliwość kontroli głębokości wypełniania z maksymalną głębokością wynoszącą 18 mm i może produkować tabletki o średnicy do 20 mm i grubości do 6 mm. TDP 5 nie skazuje Cię na produkcję tabletek o regularnych kształtach. Wystarczy zmienić formę w urządzeniu, aby być w stanie produkować tabletki o najróżniejszych kształtach. Możesz również ustawić gęstość produkowanych tabletek, a urządzenie daje możliwość stemplowania powierzchni tabletek, aby nadać im atrakcyjne wykończenie lub ułatwić ich identyfikację. Biorąc pod uwagę popularność TDP 5 w projektach badawczych, wielu użytkowników zauważa, że wymienione wyżej funkcje są bardzo pomocne, ponieważ umożliwiają produkcję małych ilości tabletek o różnych składach w celach testów klinicznych.
Tabletkarka jest kompatybilna z większością granulowanych i sproszkowanych surowców, ale nie służy do wykorzystywania bardzo mokrych materiałów ani bardzo drobnych proszków.
TDP 5, zaprojektowana z myślą o wygodzie, jest bardzo praktycznym urządzeniem, które można zasilać prądem lub ręcznie. W trybie ręcznym tabletkarkę zasila się obracając koło obrotowe. Ta elastyczność użytkowania, połączona z małymi wymiarami i niską wagą jak na tabletkarkę o takich specyfikacjach, sprawia, że TDP 5 jest bardziej uniwersalna i przenośna od innych urządzeń oferujących podobne osiągi.
Specyfikacja techniczna
Wymiary tabletkarki TDP 5 wynoszą 700 mm x 400 mm x 800 mm, a jej waga 125 kg. Szybkość wynosi 1400 r/min gdy działa na elektryczność, a maksymalna moc silnika wynosi 0.75 kW w przypadku podłączenia do jednej fazy i 0.55 kW w przypadku trzech faz. Urządzenie może działać przy napięciu wynoszącym 110v lub 220v.
Użytkowanie tabletkarki TDP 5
Tabletkarka jest bardzo łatwa w użyciu, a mimo małego rozmiaru oferuje wiele zalet, które wyróżniają ją spośród porównywalnych urządzeń.
Aby napędzać tabletkarkę ręcznie, wystarczy, że włożysz surowce do zbiornika w kształcie rożka, a następnie chwycisz za koło i zaczniesz je delikatnie obracać. Pojawią się wtedy wykonane przez Ciebie tabletki, już gotowe do włożenia do opakowania. To bardzo prosty proces, którego każdy może się szybko nauczyć. Jeśli chcesz wykonać jedynie kilka tabletek ta prostota jest zaletą samą w sobie oraz główną cechą urządzenia. Jeśli potrzebujesz wyprodukować większą liczbę tabletek, wystarczy, że podłączysz urządzenie do prądu, dzięki czemu będzie działała płynnie i szybko.
Opracowywanie i testowanie tabletek wymaga często stworzenia tabletek posiadających podobne, ale jednak odrobinę różniące się od siebie, składy. TDP 5 posiada kilka cech, które sprawiają, że jest doskonale przystosowana do takich działań.
Po pierwsze, to bardzo efektywna tabletkarka, która dzięki niewielkiemu zużyciu surowców pozwala na wyprodukowanie większej liczby tabletek z określonej masy materiału. Po drugie, szczególną zaletą TDP 5 jest możliwość pracy z minimalną ilością materiału wynoszącą jedynie 200 g. To świetna wiadomość dla działów badawczych, bo pozwala na produkcję jedynie kilku tabletek w celu przeprowadzenia wstępnych testów. Później, gdy już zidentyfikujesz obiecujący skład, możesz używać TDP 5 do produkcji większej liczby tabletek do dystrybucji podczas testów.
Po trzecie, TDP 5 pozwala na zapewnienie wydajności procesu testowego poprzez zapewnienie, że produkowane przez Ciebie tabletki można z łatwością rozróżnić. To bardzo ważne, aby mieć pewność, że prawidłowa formuła została podana odpowiedniemu testerowi. TDP 5 może sprostać temu wyzwaniu dzięki łatwości, z jaką można zmieniać kształt, rozmiar i wzór tabletek. Jeśli tylko posiadasz formę do tabletki, którą chcesz stworzyć, możesz szybko zmienić design usuwając zbiornik i odkręcając podajnik.
Możesz również szybko dopasować gęstość i wagę produkowanych tabletek - wystarczy, że odkręcisz nakrętkę na pręcie łączącym i ustawisz odpowiednią siłę nacisku.
Konserwacja TDP 5 nie wymaga wielkiego nakładu sił, wystarczy dwa razy w miesiącu dokonać przeglądu, naoliwienia i smarowania części ruchomych. Urządzenie zaprojektowano w taki sposób, aby utrzymanie go w dobrym stanie było bezproblowe.
Nasza opinia
TDP 5 to świetna jakość w dobrej cenie. Oferuje niedoścignioną uniwersalność. Łatwa konserwacja i możliwość ręcznej produkcji niewielkiej liczby tabletek sprawiają, że urządzenie jest bardzo łatwe w użyciu, zaś możliwość zasilania prądem i produkcji większej liczby tabletek - do 5.000 na godzinę - daje dwie maszyny w jednej. Nic dziwnego, że TDP 5 to jedna z najpopularniejszych tabletkarek tej klasy.
Nazwa | WartoÅÄ |
---|---|
Produkt | TDP-5 |
Liczba gÅowic | 1 |
Maks. siÅa nacisku (Kn) | 50 |
Maks. Årednica tabletki (mm) | 20 |
Maks. gÅÄbokoÅÄ napeÅnienia (mm) | 18 |
Maks. gruboÅÄ tabletki (mm) | 8 |
Maks. produkcja na godzinÄ | 5400 |
Liczba stacji napeÅniajÄ cych | 1 |
Podwójnie powlekane tabletki | Nie |
Silnik (KW) | 0.55 |
Liczba faz | 1 |
AMP | 5.7 |
Wolty | 240v (110v na zamówienie) |
WysokoÅÄ (mm) | 800 |
SzerokoÅÄ (mm) | 400 |
GÅÄbokoÅÄ (mm) | 700 |
Waga (kg) | 132 |
Net Weight (kg) | 132 |
How Much Profit Will This Machine Generate?
Are you able to calculate the amount of profit your business generates per tablet? If so, this calculator will be able to tell you how many hours you will have to run this tablet press to cover its investment.
It will also be able to tell you the amount of profit it will generate every hour you run this tablet press, which makes this calculator a powerful tool when deciding on which tablet press is right for you or your business.
Profit Generated Per Hour
This machine returns it's investment in hours
Yes. Some of them. There are a number of parts that are able to be changed between the different TDP ranges. This includes the tooling, a lot of the upper and lower drift pin assemblies and the boot bolt and spring.
No, the TDPs are not CE certified. To acquire this certification, they would have to be installed in a protective cage, which we do not provide.
Yes, you can change the tooling. It is fairly easy. It takes about an hour or so the first time you do it, but you will get quicker. An LFA technician can do it in around 10 minutes - practice makes perfect!
Here is a video link on how to change the tooling: How To Change A Die | Changing a TDP Tablet Press Punch Die
The tooling does wear out. How long this takes will depend on your product formulation. The more granular it is, the faster your tooling will wear down.
Yes, you can, but there are a number of requirements that we need to fulfill first.
You will need to contact our team and provide them with a copy of all of your MSDSs for all of the components of your mix.
We need to have a good understanding of your business and the challenges you are facing.
You will also need to book an appointment with the office that you would like to visit.
For more information please get in contact with the team: https://www.lfatabletpresses.com/contact
No, sorry. We are only able to offer them in one colour. It is important to point out that the colour in the photo might vary slightly from batch to batch of machines.
Yes. Very easily.
We have free lifetime technical support for all machines sold by LFA.
Just contact us with your machine serial number and we would be happy to help you with any problems.
Yes, just give us a call and we will check our stock levels. We aim to hold the TDP 5 in stock for our customers however there are some times when it does go out of stock, so it is worth calling.
If we have it in stock then it will take around 2-5 days to deliver to you depending on how far you are from our nearest office.
When operating a desktop tablet press, supervision is required at all times. From time to time, excess powder can build up and cause tablets to form where the front of the boot gets to in its ejection cycle. When this happens there is a chance that a tablet could roll back into the way of the upper punch coming down to make a second tablet.
If this happens the addition of the two tablets together in the press will cause a jam that is very hard to undo.
If the machine is not turned off in time then the motor can burn out causing serious damage to the press.
It is also possible that your mix will stop flowing while running the machine. This will cause you to get underweight, soft tablets that will then have to be picked out, broken down, and reworked.
Yes, you can, but most people would not. There are a few technical challenges that exist with making effervescent tablets that do not exist with other forms of tablet that the TDP 5 is not well suited for.
Most effervescent tablets tend to need to be quite large. As the TDP 5 is not great at making a tablet over 14mm this would be a problem for most people.
If the size is not the problem then the tooling could be. Effervescent tablets tend to have quite high ejection forces and are prone to sticking to the punches. To combat this, we would normally create tooling with PTFE inserts and tungsten carbide lined dies. This would make the one set of tooling for the TDP quite expensive and not only that but there is a minimum order quantity of 5 sets when ordering custom tooling.
Yes, the contact surfaces are all food and pharmaceutical safe.
They are made from a combination of, stainless steel, chrome coated brass and the steel used for your tooling (often S7).
As such they are all compliant with most rules for food or pharma manufacturing.
We strongly recommend that you check your local laws as these do vary from state to state and country to country. If in doubt reach out, and we will be happy to find out.
Yes, you can.
You are able to make any shaped tablet up to the maximum diameter of this tablet press which can be found under the "specifications" tab.
We are able to customise tooling to include lettering, numbering and logos. If you would like customised tooling please fill out our custom tooling form: www.lfamachines.com/custom-tooling
Yes. You can order custom tooling here
No. It is technically possible for us to make tooling that is less than 4 mm however, the TDP does not really have the tolerances for the tooling to work properly with most mixes, so we do not recommend it.
No. The TDP 5 is a single station tablet press. The RTP range is a rotary tablet press. The way that they work means that it is impossible to move the tooling from one to another.
No. The fill depth of the press is 18mm.
No. The way that a single station press works is that it runs in a single rotation. To put in a pre-pressure compression, you would have to stop the press and then reverse it. This really would not work. If this is something that you feel you need then it is best to look at rotary tablet presses. If pre-pressure is something you need, look towards our RTP 10i Rotary Tablet Press.
Yes, but not pharmaceuticals it is not compliant with cGMP standards.
If you need a cGMP compliant machine then the best desktop for this is the DTP 12 or 25. LFA is of the understanding that the TDP 5 can be used to make food products and supplements.
It is worth checking with your local food regulators if they have recommendations as to cleaning procedures. It is also worth inquiring about their specific regulations as each territory and regulating body has slightly different requirements.
No.
LFA does not recommend leaving any of its machines unattended without an operator ever. Even if they only need to step away for a short amount of time, the operator should turn off the machine.
This will avoid damaging it in the event that there is a jam and the operator is not there to switch it off.
No, sorry, we do not customize our products. We only offer machines that are shown on our website. We do this so that we can be confident about the machines we sell and our ability to support them properly.
No, if you would like to adjust the speed of your TDP 5 you will have to do so using a variable speed adjuster.
There are off the shelf versions that the TDP can plug into. You need to make sure that it is set up for the right electrics for your motor.
Yes, the TDP and RTP range all have a weight adjustment for it.
on the TDP it is the bottom of the two cogs on the lower drift pin assembly.
Here is a link to a video showing you how to tune up the TDP 5: https://www.youtube.com/watch?v=4dTscUdRJzQ
Here is a link to a video showing you how to tune up the RTP 9 or the RTP 118: https://www.youtube.com/watch?v=YJFt5AFJ1hw
It is important to know that the exact weight of each tablet will vary from tablet to tablet.
A well-homogenized mix that has a consistent granule size should be able to achieve an accuracy of +/- 3% or less.
Yes, you can request multi-tip tooling for your TDP5, but there are a few things to consider first. Because the maximum tablet diameter size on a TDP 5 is 20mm, all of the punches would have to fit into this space, resulting in very small tablets. In addition to smaller tablets, it would not be cost effective since the cost of multi-tip tooling is the same amount as a second machine.
It is important to remember that the TDP 5 is sold as an R&D and small batch machine. If you are looking to do large runs then you might want to consider an RTP rotary tablet press.
It is important to know two things:
Firstly, TDP Universal Tooling came into effect in 2018. Machines brought from LFA before this time may be slightly different sizes. We always recommend checking the size of your tooling before placing your order.
Secondly, a number of companies make unofficial TDP tablet presses.
They do not always conform to the same sizes, tolerance or quality as LFA TDPs or tooling. If you bought your press from someone else other than LFA, we are not able to guarantee that our tooling will fit.
Yes, you do get a die with the machine. Every machine comes fitted with a die.
If you would like you can get this customised with your logo or lettering but it takes 6-8 weeks.
Or, we have a standard 8mm round, bevelled edge with breaker installed in the machines in stock.
That depends on the country you are located in.
In the EU and UK no. You do not need anything to buy the press.
In the USA we have to file a piece of paperwork with the federal government when we sell the press.
We, however, do all of this paperwork for you and do not need to do anything.
The only countries that require a license, as far as we know, are Canada and Australia.
If you are located in Canada then we recommend that you contact Health Canada prior to placing your order. Details regarding the import process can be found at the following link: Importing and registering pill presses (designated devices)
The document you need to fill out and file for a purchase originating in Australia is called a B712. This can be found at: https://www.abf.gov.au/form-listing/forms/b712.pdf. If you would like to speak with one of our team about this, then please get in contact.
No, an allen key set, a spanner set, and a crosshead screwdriver will cover most of the operations that you should ever need to do. Even to do a full strip down and assembly there are no specialist tools that you would need that a local hardware store would not be able to provide.
No. Sorry. If you would like it in another language, we would be happy to get it translated for you. Simply reach out to the LFA team and we will work to get it done. Please note that this could take a while and we are not able to guarantee if we will be able to get it done.
No, it does not need to be bolted into position but we do recommend it. If the machine is not secured in position by bolts or another method then it is more likely to shake a bolt loose, resulting in varying tablet weights. On top of this, the vibrations are likely to make the machine sound louder.
The machine does not come with bolts because we do not know the thickness of your surface.
Tak, możemy przeprowadzić dla Państwa szkolenie w naszym biurze w Bicester. Trwa ono około jeden dzień.
Yes, you can definitely make shaped tablets in the TDP 5. It is harder to tune, but it is definitely possible.
No, at the moment we have not done any reliability testing on the TDP 5. LFA, however, has 10 years experience selling, maintaining and servicing the TDP desktop press so we are sure of its reliability.
This feature is not available on the TDP 5. The TDP 5 is a basic machine that is priced accordingly. If you need to know the amount of pressure that you are using to make one of your tablets you might want to consider an RTP 10i or HSTP.
The TDP 5 is cleaned in the same way as any press. We recommend 6 separate steps:
Removal of Powder - Start at the highest point of the machine while it is still assembled. Hoover out the residue powders using a paintbrush to dislodge any powders trapped in tight areas.
Remove the hopper, boot, base plate and tooling.
Apply Soap - Wash the entire machine with warm soapy water. Making sure to pay extra attention to all of the contact parts. Do not soak the machine, rather apply it with a cloth or sponge and then wipe it dry as you go.
Sanitise - use a sanitising spray or wipe to clean down the entire machine making sure you pay close attention to all contact parts.
Rinse - Next rinse off any soap or sanitising spray with potable water. Making sure not to soak the machine, rather apply it with a cloth or sponge and then wipe it dry as you go.
Oil and Lubricate - Finally to prevent rust and keep the machine running smoothly lubricate.
We would recommend that you do this at the end of every production run or day that you have been using the machine on. We would also recommend that you store the machine under a dust cover and in a cool, low humidity environment to prevent rust.
More information on cleaning and maintenance for the TDP 5 can be found here:
We have a tool called the right machine for you. It can be found here: Right Machine For You - Questionnaire
The upper drift pin assembly is used to adjust the pressure. You can watch a video on this here: www.youtube.com/watch?v=pc2gfDU3NiQ
Here is another video which tells you how to set up a TDP ready to press: www.youtube.com/watch?v=4dTscUdRJzQ
There is a bolt eyelet on the top of the machine.
We recommend using an engine hoist to lift the machine off the shipping crate and into the position that you are going to use it in.
We have self certified it under the part finished machines regulations. You will need to set up the environment around the press in a way that finishes satisfying the CE requirements.
The TDP 5 is a very small machine that can be cleaned in as little as an hour.
More information on cleaning your TDP 5 can be found here:
LFA is aware of customers who have been able to run their TDP 5 for 10 hours a day, several days in a row. However, LFA does not recommend this, because it will wear the machine down. It is important to let it cool and to clean and grease it regularly.
Not a lot. We have a number of videos on our website that do cover the basics. If you would like to have in person training, then this is something that we would be happy to offer. It is free for anyone that has bought a TDP 5 from LFA and available at any one of our three offices. This takes around 2-3 hours.
We would recommend cleaning down the machine and leaving it re-greased after every use. This will ensure the longest life possible.
Here is a video on cleaning the TDP 5.
When greasing the machine, avoid getting any grease near the tooling or pressing surfaces, as this will get into your tablets and affect your powders.Grease the top cam well, then apply a small amount to the upper drift pin assembly and the lower timing rod.
More information on greasing your machine can be found here: TDP 5 Lubrication Schedule
We would recommend doing a full clean down and re-greasing at the end of every production run. This takes about an hour and will dramatically increase the life of your press.
Bardzo szybko. Średni koszt produkcji tabletki u producenta to 10 – 20 groszy w zależności od stopnia trudności kompresji oraz nakładu. To oznacza, że koszt tabletkarki TDP 5 zwróci się po produkcji 380 tysięcy tabletek. Sprzęt produkuje średnio 5 tysięcy tabletek na godzinę, co oznacza, że tabletkarka TDP 5 potrzebuje… 76 godzin na zwrot kosztu zakupu.
This is a common question, and we have tools to help you:
A video on the differences between the different TDP's - www.lfatabletpresses.com/videos/tdp-range
The Right Machine For You Questionnaire - https://www.lfatabletpresses.com/tablet-press-questionnaire
These will explain the different machines, and give you a much better idea. If you are still unsure, please do reach out, let us know what you are making and the quantity, and we will help to guide you through the process.
We don’t have a template available at the moment. You can measure the distance between the holes in your machine’s base to determine where to drill holes on your workstation. The tablet presses include the M10 bolts that we use to secure them to the shipping crate, so we would recommend using a 12mm drill bit.
There are a number of times when it would be better to get a TDP 5 instead of a TDP6. Really a TDP 6 is only better if you need to make shaped tablets (not-round) very regularly or if you need to make very large tablets (bigger than 12-14mm).
If this is not the case then the TDP 5 is lighter, faster, and costs less than the TDP 6.
The TDP 5 tablet press is 85 decibels, so it's not excessively loud. We would, however, recommend using ear protection if you are going to be using it for extended periods of time.
Yes, we are currently designing a perspex box that covers the entire machine. It will be sold as an optional extra.
In order to determine whether or not your machine is still under warranty, you will need to call or email the office the machine was purchased from, and provide the serial number.
Yes, the press does have a variable speed control. It can be run between 10-50 RPM.
This speed control is varied using a variable adjuster and the speed is shown on an LCD readout.
Note: It technically can be run slower than 10 RPM but the press is likely to not have the kinetic motion to complete the compression of a tablet.
It will depend on the model. All new models of the TDP 5 have emergency stop buttons.
There are three things that could be causing this fault:
The motor is burnt out. If this is the case the motor will be slow to start if it starts at all. It will be really hot and it will make a grinding noise.
The punches are not in the die. If the top punch is not aligned or the bottom punch is not securely in the die bore then the machine will perform a 1/2 rotation before jamming.
The machine has not been greased correctly. If this is happening then the machine might run for a full turn or maybe even a few and then it will jam. This happens as the cogs, cams and bushings heat up and expand until they jam. The most likely place this is happening will be on the pinion gear. It is critical that this part is well lubricated.
Yes, this could be down to corrosion or due to oxidation of your product. We would highly recommend taking your tooling out of the press and cleaning it at the end of every production run.
We would also recommend polishing the tooling to keep the surfaces clean and less likely to cause picking or capping.
Yes, this can happen because the boot bolt and spring have been screwed too far into the press or have not been screwed in far enough. It is important to make sure that the bolt is in the correct position before over tightening the set screw.
It should be pointed out that it will not affect the operation of the press if it is damaged.
We would recommend securing the TDP 5 in one of three ways:
Anti-vibration feet. These work great, they are large rubber pads that can bot through the 3/4 holes on the bottom of the press. They reduce the amount of noise from the machine and the rubber pads will stop it from slipping around.
G-clamps. An easy way to secure the tablet press to a table top without doing any damage to the bench top is using G-clamps. These are available from most hardware stores and are easily able to pin the machine to the work surface securely.
Bolt the press to the worktop. We would only recommend this if you really are sure of the location that you would like it to be secured. If you do want to do this then you can use the bolts that were sent with the press that was used to secure it to the shipping container.
The TDP 5 has a safety cover over the drive cog to protect you when it is running. There is also an accessible off button, to manually shut the machine off.
That would depend on the product you plan on producing, the requirements of your local authorities, and the governing bodies of the product that you are making. We would however strongly recommend installing it in a cage.
We would recommend a batch of around 5,000 once per day.
It is a balance. If you stop and start the motor then you are likely to wear it out. If you run the press for long periods of time then as it heats up parts will expand the grease will thin and the wear on the machine will increase.
The largest tooling that the TDP 5 can take is 22mm however at this point the amount of pressure that you are able to get is very low. This is because the boot is not able to move out of the way of the die as it comes down.
This will be affected by your mix. Most mixes will not have the density required to work with such a thick tablet and low amount of compression.
Because of this at LFA we do recommend that you only try to make a tablet of up to 14mm on the TDP 5. If you do need to make a bigger tablet then we would recommend using a TDP 6s or one of the RTP range of rotary tablet presses.
To bardzo częste pytanie, gdyż te urządzenia są bardzo podobne, jednak posiadają różną moc.
Można natomiast je podzielić na automatyczne i manualne.
Tabletkarka pulpitowa TDP 0 jest modelem manualnym i wymaga ręcznego uruchamiania w trakcie produkcji. Posiada najniższą siłę nacisku i jest swego rodzaju modelem początkowym tabletkarek TDP.
Tabletkarki TDP 1.5, TDP 5 oraz TDP 6s są urządzeniami automatycznymi zasilanymi przez silnik elektryczny. Tabletkarka TDP 1.5 jest modelem początkowym urządzeń automatycznych. Posiada najniższą siłę nacisku równą 15 kN i ograniczony zakres rozmiaru tabletek. Tabletkarka TDP 5 jest naszym najpopularniejszym modelem i może wyprodukować około 5 tysięcy tabletek na godzinę. To urządzenie posiada siłę nacisku równą 50 kN i może produkować tabletki o średnicy do 22 mm. Tabletkarka TDP 6s jest najbardziej zaawansowanym urządzeniem odpowiednim do produkcji niestandardowych rozmiarów tabletek. Posiada również nieznacznie większą siłę nacisku równą 60 kN, co może się przydać w produkcji tabletek, których skład trudno jest skompresować.
22mm is what we say, although we have seen a customer successfully use a 27mm oval die on a TDP 5. This being said, the bigger the die the harder it becomes to use the press. The better you mix will need to be and every other factor will need to be in your favour. We do not recommend using a TDP 5 press a tablet above around 14-16 mm unless you have had your formula tested first. The ideal size is less than 12mm.
Spare parts are held in stock in the UK, USA and Taiwan. This means that we can normally dispatch them in 1-2 days. Shipment delivery times will vary depending on your location.
The length of the warranty on any of the TDP range machines is 1 year from the date of purchase.
This warranty covers spare parts and excludes tooling and maintenance labour from LFA for machine services.
When you receive your machine, you will be given a serial number that will also be stamped onto the press. You will be able to use this if you ever need to make a warranty claim.
Full details on the LFA warranty can be found here: Warranty | We Have You Covered
The TDP 5 is an incredibly hardy little machine.
Not only that but it has a very basic mechanical process. While parts can break and wear over time the cost of replacing them is normally very low. We have known customers to have done 100,000’s of tablets on the TDP 5.
This having been said it is still just an R&D and small batch machine. We would not recommend using it for making large batches.
The reason for this is that it is slow at only 5000 per hour and if you do run it constantly then you are going to be replacing a lot of parts on it. The life of the TDP 5 can easily be in the millions of tablets if well looked after and maintained.
There are a number of advantages of the TDP 6s over not only the TDP 5 but all of the other TDP presses. The main one is how easily it is to press shaped tablets. It is able to do this because of the way that it adjusts the punch pressure on the machine. It does it using a linear motion rather than a rotational motion.
A video of how to adjust the pressure can be seen here:How to Adjust the TDP 6s or 7 Tablet Press Punch Pressure
As with all machines, the TDP 5 will have parts on it that over time will need to be changed or that can become damaged through user error. Below is a list of parts that LFA has come to recognise as the most frequently damaged or that have been designed to wear so that more expensive parts of the press are protected.
Tooling - The tooling on the TDP 5 can become chipped or broken. Lead times for a new set of tooling can take as long as 6-8 weeks so we recommend having a spare set or two. This is especially true if the tooling is customized.
Boot - The TDP 5 boot is formed from a toughened food grade plastic. This part can become trapped between the die bore and the upper punch and usually happens from user error when the upper punch has not been secured correctly. While we hold this part in stock at all of our locations it can reduce waiting to have a spare.
Boot Timing Bar - In the event that the boot is trapped or damaged by the upper punch the boot timing bar can become bent. While we hold this part in stock at all of our locations it can reduce waiting to have a spare.
V Belt - The V Belt on the TDP 5 is used to drive all of the power from the motor to the cams. This overtime will lose some of its tension and wear. When this happens the maximum pressure that you will be able to achieve on the press will reduce. We do hold this part in stock and most of the time the part will not fail, requiring immediate replacement. The tension on the belt can also be increased by adjusting the position of the motor. This will extend the life of the belt.
Upper Cam Bushing - The upper cam bushing is a brass wear part that is used to keep the upper cam from coming into direct contact with the base of the machine. This part will need to be replaced after around 500 - 1,000 hours depending on the product being pressed and the pressure being used.
The expected life of your tooling will depend on a number of things. The most important is how granular your mix is. It will also depend on what steel grade you have opted to have your tooling made from and if it is coated. Because of all of these factors, it is almost impossible to predict how long your tooling will last.
Tabletkarka pulpitowa TDP 5 jest od pewnego czasu najpopularniejszym modelem. Część z klientów wraca do nas po zakup tabletkarki rotacyjnej RTP 9 (zazwyczaj po kilku latach), jednak większość zaczyna od tabletkarki pulpitowej TDP 5.
On the TDP 5 Version 2 the contact parts are made from, stainless steel, food grade plastics and the steel that the tooling is made from. The tooling that comes with the machine is made from S7 steel. If you need a different steel type for your tooling, you can place an order using our custom tooling form:https://www.lfamachines.com/custom-punch-dies-tooling
As with any tablet press, it is good to have a particle size of around 80-60 mesh.
This would be large enough to avoid large losses and small enough to flow well through the machine. If the powder is finer than this then you are going to experience a larger level of loss.
If the particles are larger than this then it might not flow through the machine well and get caught as it is trying to enter into the die bore.
This being said every powder is very different and you will need to do tries to work out what is best for them.
The most common part that gets broken is the boot followed by the lower assembly timing rod runner bolt. We hold both of these in stock.
A common reason the boot needs to be replaced is that the upper drift pin assembly was not locked in place. As the machine runs, it works itself loose and then over a few tablets, it comes down and hits the boot. This can also happen if the operator does not turn over the TDP 5 by hand to tune the machine before turning the motor on, causing the upper pin to crash into the boot.
A common reason why the lower assembly timing rod runner bolt tends to break is because the tablet ejection forces are high. To reduce this, the operator should ensure that the mix is correctly lubricated.
We send out all machines with the local plug on and set up to run on the local power supply.
We would recommend using goggles, a dust mask and gloves at a minimum, but you may require a lot more depending on the products that you are working with, and your local health and safety laws.
Get a capsule filler.
You will not be able to make tablets.
Click here for more information https://www.lfacapsulefillers.com/
The TDP 5 has been designed to the CE standards.
There are a number of ways we are able to support you:
- Every machine comes with a full manual that is emailed to you after purchase.
- There is a large range of video tutorials to teach you how to use the press.
- The machine comes with lifetime technical support. You can call, Skype or email to get answers to your questions and problems.
- We also offer free training at any one of our regional offices.
If after all of this you are still struggling to use your press, we are able to come to you. This is a service we charge for.
More information on this can be found here: https://www.lfatabletpresses.com/services
The tension on your TDP 5 belt will depend on whether or not you are installing a new belt or tension on an old one. Here are the exact tensions for the TDP 5:
Installation strand tension for new belt [N] 141.64
Installation strand tension for run-in belt [N] 94.42
To measure the tension on a belt we use a tension pen gauge. Here is a link to a video on how to use the belt tension pen gauge: Browning Tensioning V Belt Drives
Deflection forces for belt tension pen gauge [kg]
New 0.98
Run 0.67
All of our machines are made by us in Taiwan, and are shipped to you from our nearest office.
We have offices in the UK, USA, Germany and Taiwan.
Because they are made by us, we are able to control quality and give you the best support possible. And because they are shipped from your local office, wait times are reduced and customs clearance is avoided, ensuring you have support in your time zone in a language that is convenient to you.
The TDP 5 and the TDP 6s are both able to take shaped tooling. This being said, it is a lot easier to use shaped tooling on the TDP 6s because of the way that the pressure is adjusted.
The most common part to wear out on the machine is the boot. This comes in direct contact with the die cavity and can be hit or chipped by the upper and lower punches. This is made of brass so that the tooling is protected in the event of a collision. Because of this, the boot is soft and will wear over time. If anything, we recommend keeping a spare to avoid losing production time.
We also recommend that you keep at least 1 spare set of tooling as this can break or wear over time.
LFA aims to hold all major spare parts and tooling in stock so that they are ready to ship out in the event that you need them. The lead times on sold out parts, however, can take up to 6-8 weeks
Almost, you will have to attach the hopper. We leave this off so that it does not get damaged in shipping. This should take less than a minute. The machine will then be ready to run. It is important that at that point you tune the machine by hand and do not turn it on right away. If you do, it can damage the press. Here is a video on how to tune the TDP 5: Setup the Fill Depth, Punch Pressure & Ejection Height on a TDP 5 Tablet Press
We also have a video on unboxing your TDP 5 here:TDP 5 Unboxing & Setup
There are a few interchangeable parts if both machines have been made by LFA Machines. From the TDP 0, this includes the tooling, the lower drift pin assembly, and its corresponding set of cogs.
The most important fit to check for is tooling that you may have previously purchased, because the base plates have been redesigned to fit the universal standard tooling die.
More information on the TDP Universal Tooling Standard can be found here: Tooling | Punch & Dies for TDP Pill Presses
All other parts are custom to this press.
There are three reasons to granulate your formula:
1. To improve the flowability of your formulation.
2. To make your formulation more compressible.
3. To ensure a consistent spread of API throughout the formulation.
If you would like to find out if your mix needs granulation then we do have a tablet formulation service available.
You can find out more about the tablet formulation service here: https://www.lfatabletpresses.com/services
Yes, our 1 year warranty covers all of the parts on the machine, except for the tooling. If you install it in a cage to conform with CE regulations, then this will in no way affect the warranty.